Laboratoire de freinage de Bosch
Visite chez le cuiseur des plaquettes de frein
17 decembre 2024 agvs-upsa.ch – Les freins freinent ? Ce n’est pas si simple : les plaquettes de frein sont un composant automobile sous-estimé. Chaque plaquette de frein du marché de la rechange représente des années de développement – et parfois même du bois de hêtre. Nous visiterons en exclusivité le laboratoire de freinage de Bosch, le numéro un mondial des plaquettes de frein. Timothy Pfannkuchen
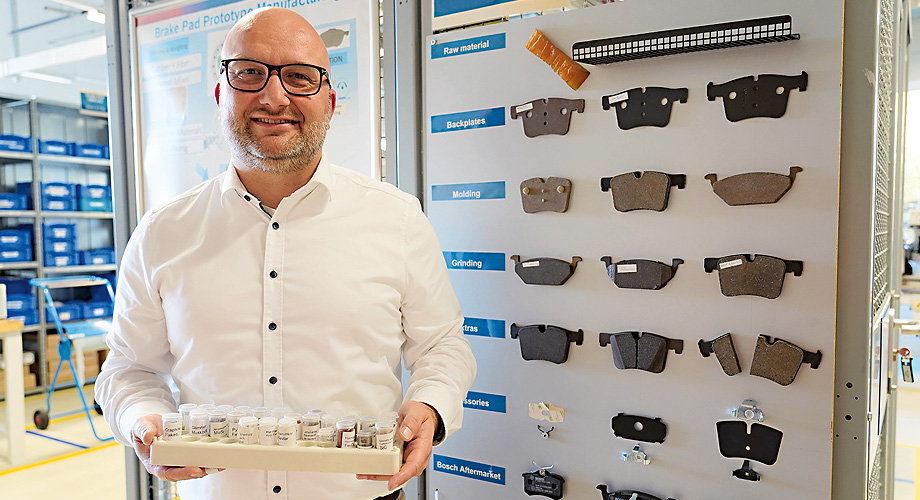
Là où naissent 10 000 types de garnitures de frein : dans le laboratoire de freinage Bosch, Andreas Mayer, responsable de la zone de produits Freins Aftermarket, explique les processus. Et montre quelques-uns des 15 à 25 composants possibles d’une plaquette de frein. L’un d’entre eux est par exemple le bois de hêtre. Photo : médias de l’UPSA
Votre carte d’identité, s’il vous plaît : avant d’entrer dans l’épicentre du marché de la rechange de Bosch à Karlsruhe, en Allemagne, il faut d’abord franchir les obstacles de la protection de l’usine. Avec amabilité et dans la langue de Baden, nous sommes identifiés, photographiés, formés et signons toutes sortes de papiers. Elles disent : tout est secret ici. Le fait que nous puissions tout de même entrer et même prendre des photos – toujours après consultation, s’il vous plaît – est une exception exclusive. Car nous visitons ce qui ne se visite pas vraiment : le laboratoire de freinage de Bosch.
Le laboratoire de freinage se cache dans l’ombre de l’entrepôt central de l’aftermarket et porte le charme architectural d’une école primaire des années 1970. D’une certaine manière, c’est aussi très Robert Bosch GmbH : être au lieu de paraître ; dans ce bâtiment insignifiant d’un étage, ils en ont gros sur la patate en matière de technologie. Je m’appelle Andreas Mayer. Une poignée de main ferme et la ferme conviction que freiner, c’est bien plus que ralentir. Le titre officiel de la fonction de Mayer est « Product Area Owner (VP) ». Je vois. « Responsable de la zone de produits Freins Aftermarket », explique Mayer en souriant. En bref : Mayer est le chef. Et comme beaucoup ici, un vrai « Boschien » : stage, thèse, carrière – 20 ans de service. Ce natif de Hanovre n’a pas adapté le dialecte local, mais l’attitude locale : quand Bosch fait quelque chose, il le fait bien.
« Mieux vaut perdre de l’argent que de la confiance », comme l’avait dit autrefois Robert Bosch (1861 à 1942). Et a fondé en 1886, l’année de naissance de la voiture, l’entreprise qui a mérité cette confiance par la qualité – et parl’innovation. Le servofrein (1927), l’ABS électronique (1978), l’ESP qui en découle (1995) : toutes des premières mondiales de Bosch. Aujourd’hui, Bosch est le plus grand équipementier automobile au monde et le numéro un des systèmes ABS, par exemple. Etonnant : pour les plaquettes de frein (sur lesquelles nous nous concentrons ici), Bosch n’est pas un équipementier de première monte. En revanche, elle est le leader mondial des plaquettes de frein pour le marché de la rechange et, en Europe, des disques de freinage. Le programme de l’aftermarket comprend 46 000 articles de freinage. Parmi eux, des dizaines de liquides comme le nouveau DOT 4 E, un liquide de frein universel sans borates nocifs pour la santé et qui n’est donc plus une matière dangereuse. Ou 10 000 types de plaquettes de frein, couvrant 97 % du marché. Pour qu’il en soit ainsi, il y a trois laboratoires de freinage avec 120 collaborateurs : en Chine, aux États-Unis et au siège de l’aftermarket à Karlsruhe, en Allemagne.
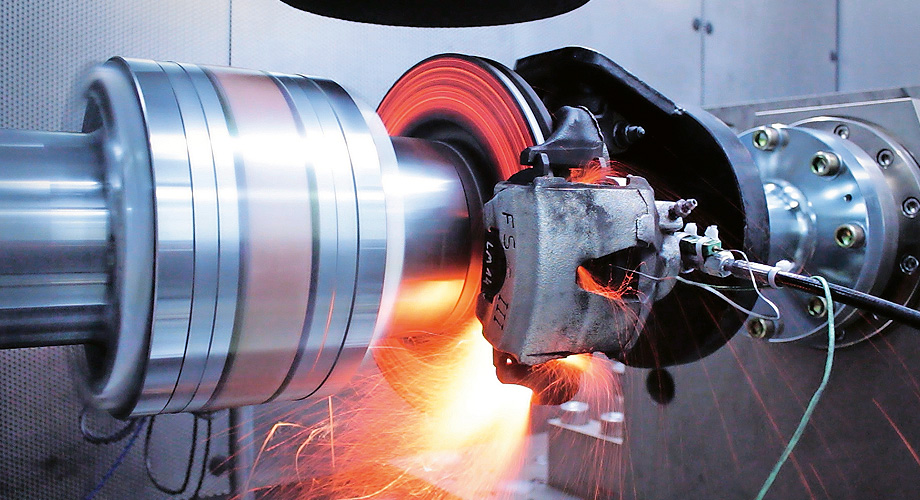
Tester jusqu’à ce que les disques de freinage soient littéralement incandescents : dans le laboratoire de freinage, les disques et les plaquettes sont soumis à de nombreux tests avant d’aller sur la route pour des essais réels. Les tests portent par exemple sur la résistance au cisaillement des revêtements, les vibrations et bien sûr les valeurs de frottement, c’est-à-dire de décélération. Photo : Bosch
Cuire des plaquettes de frein dans la cuisine
« C’est un peu comme la cuisine : au début, il y a les ingrédients », dit Mayer, 46 ans, avec un clin d’oeil, avant de nous conduire au laboratoire. Des creusets et des pots, des instruments scientifiques : ici, on analyse, on expérimente, on compose. Une cuisine dans laquelle l’équipe de Mayer assaisonne de nouvelles plaquettes de frein. Le développement de la plaquette de frein n’est-il pas terminé depuis longtemps ? Mayer nous regarde brièvement, comme si nous avions posé une question indécente, et répond : « Si nous arrêtions, nousserions hors du marché au bout de trois ans. Le frein est un élément sous-estimé. Une plaquette de frein est composée de 15 à 25 matériaux, et bien sûr, nous améliorons continuellement ». Qu’est-ce qu’il y a dedans ? Des métaux comme le fer ou le laiton, des choses imprononçables comme le sulfure de molybdène, souvent de l’aramide, du graphite, du kevlar, auxquels s’ajoutent des fibres de verre ou de caoutchouc et, pour ainsi dire, comme colle, des résines synthétiques et naturelles. « Et parfois du bois de hêtre », dit le cuiseur de garnitures de frein Mayer, en souriant et en savourant notre étonnement. Le bois peut ajuster la compressibilité. En d’autres termes, lorsque nous appuyons sur la pédale, le revêtement prétendument dur comme du béton doit être un peu compressible. S’il est trop dur, il grince. Cela ne devrait pas, estime Mayer, « surtout pas dans une voiture électrique silencieuse. Les grincements ne portent pas atteinte à la fonction, mais gênent les clients finaux. Cela ne correspondrait pas à l’idée que nous nous faisons de nous-mêmes ». Donc simplement des revêtements mous ? Si le revêtement est trop mou, la sensation de nos pieds devient spongieuse. « Il faut que ça fasse du bien, et les Européens aiment que leur frein soit mordant », explique Mayer. Ce qui nous permet de commencer à comprendre le conflit d’objectifs : chaque revêtement est une quadrature du cercle de freinage.
Une fois le compromis idéal trouvé, l’équipe de Mayer n’en a pas fini pour autant : pour l’Amérique, par exemple, il faut une sensation de pédalage douce. Sans parler des dispositions légales : en Europe, on s’attend à ce qu’une réglementation vienne un jour imposer que les revêtements soient exempts de cuivre. Les États-Unis l’exigent depuis longtemps – et à l’époque, Bosch était le premier fournisseur à s’y conformer. Depuis lors, chaque revêtement Bosch est exempt de cuivre et prêt pour une réglementation européenne correspondante qui suivra probablement. Non, les tâches ne manquent jamais ici. Chaque nouveau lot d’une matière première est contrôlé quant à sa composition et chaque lot de production est testé – ce qui signifie un contrôle mensuel pour les revêtements populaires. Mayer raconte ces choses de manière sympathique et décontractée et est quasiment une encyclopédie vivante sur les freins. Parfois, il glisse même « mes freins » au lieu de « nos freins ». Chez Bosch, ils prennent les freins personnellement. Dans la pièce d’à côté, un collaborateur glisse des plaquettes de frein fraîches dans un four comme un pâtissier ses biscuits. « Comme je l’ai dit, comme la cuisine », dit Mayer en riant, « dans le laboratoirenous mélangeons la pâte, ici nous cuisons la plaquette de frein sous pression et à la chaleur dans les mêmes conditions que plus tard dans la production en série ».
Une pièce plus loin : la chambre de torture. Ici, la pâtisserie est chargée jusqu’à ce qu’elle craque, au sens littéral du terme. Par exemple, lors du test de résistance au cisaillement : quelle est la tenue du revêtement sur la plaque de support ? Si le résultat est bon, le menu de freinage se déplace dans la halle avec des bancs d’essai encapsulés de la taille d’un conteneur outremer. Dans la salle de contrôle, les courbes et les chiffres défilent sur les écrans, les images thermiques montrent les températures sur des disques de freinage chauffés à 600 ou 800 degrés, tandis que sur le banc d’essai, même les climats allant de l’Arctique au désert et les nombreux cycles de conduite jusqu’à 250 km/h stressent les freins. Dans les rayonnages en hauteur, on trouve des axes comme les étagères Billy chez Ikea. Pourquoi les tests sontils effectués entièrement avec des suspensions de roues ? « Nous devons prouver pour chaque type de véhicule que la plaquette de frein pour ce véhicule précis satisfait à toutes les dispositions légales telles que la norme ECE R90. Et bien sûr, nos propres normes, qui vont encore bien au-delà des exigences légales », explique Mayer. Deux exemples : les vibrations ne sont pas réglementées par la loi, tout comme le fading ou la durée de vie des plaquettes au quotidien. Bosch établit donc ses propres règles pour cela, le dépassement est l’objectif.

Fidélité aux détails : selon les tests, des essieux complets avec amortisseurs et autres sont parfois montés sur des bancs d’essai. En effet, chaque pièce de frein du marché de la rechange doit être exactement adaptée au véhicule spécifique.
Euro 7 et la poussière de frein
Même l’air sortant des bancs d’essai est analysé. « Euro 7 », dit Mayer de manière laconique : des valeurs limites strictes pour l’abrasion des freins sont prévues vraisemblablement en 2027. L’industrie du freinage peut-elle y parvenir ? Mayer s’abstient de toute pique à l’égard des concurrents et déclare avec diplomatie « Il y a des revêtements qui peuvent le faire. Il faut simplement commencer assez tôt. Nos revêtements peuvent le faire » Les nouvelles réglementations sont-elles nerveuses ? non, nous considérons que nous avons une responsabilité à cet égard ». Ironiquement, ajoute Mayer, la poussière de frein est un sujet de préoccupation depuis bien plus longtemps aux Etats-Unis. Mais pas pour des raisons environnementales : les clients américains ne détestent rien de plus que des jantes sales sur leur véhicule rutilant. C’est la fin de notre visite. Et pour les revêtements, les tests ? « Pas du tout », souligne Mayer en montrant l’extérieur, où la flotte de voitures, de la VW Polo au Mercedes Sprinter, est prête à partir à l’assaut du Jura souabe, du Grossglockner ou du Stelvio – parce que la réalité imagine toujours des martyres bien plus méchants que n’importe quel banc d’essai. « Lors du test sur route, nous traitons les freins comme il ne faut pas les traiter. Et il faut que ça fasse du bien. Cette partie subjective ne peut pas être quantifiée », explique Mayer. Si les plaquettes, disques et autres maîtrisent cette étape, la production en série est autorisée (ce que Bosch fait lui-même dans quatre cinquièmes des cas de plaquettes de frein). Et si ce n’est pas le cas ou si, lors d’un seul des nombreux tests, le frein ne freine pas bien une seule fois ? Tout recommence.
Au fait, combien de temps cela prend-il ? « La plupart du temps, environ trois ans ». Est-ce que cela en vaut la peine ? Manifestement : il y a quelque temps, l’UE a effectué des contrôles aléatoires. Près de la moitié des revêtements ont été recalés parce qu’ils ne répondaient pas aux exigences minimales légales. « Les nôtres n’y étaient pas », dit Mayer, l’air satisfait. Pas étonnant que tout soit secret ici : la concurrence viendrait volontiers jeter un coup d’oeil. Car chez Bosch, on brûle pour ses freins. Robert Bosch aurait certainement apprécié le laboratoire de freinage.
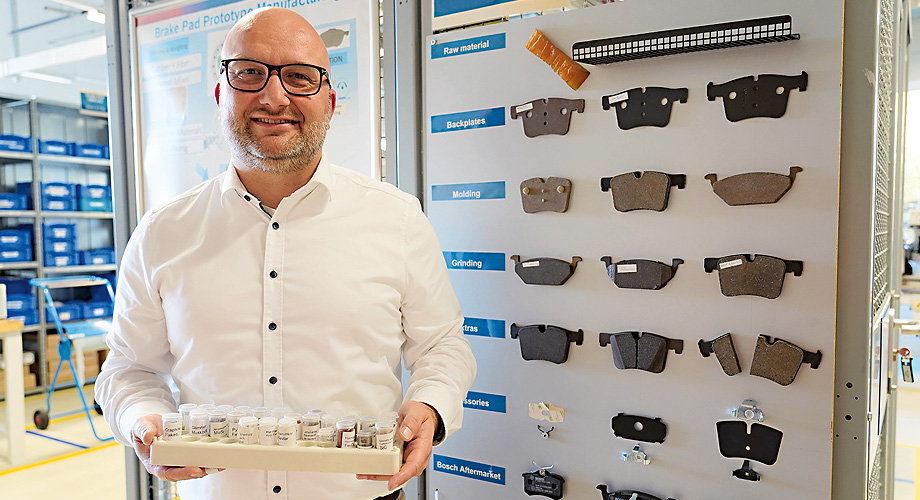
Là où naissent 10 000 types de garnitures de frein : dans le laboratoire de freinage Bosch, Andreas Mayer, responsable de la zone de produits Freins Aftermarket, explique les processus. Et montre quelques-uns des 15 à 25 composants possibles d’une plaquette de frein. L’un d’entre eux est par exemple le bois de hêtre. Photo : médias de l’UPSA
Votre carte d’identité, s’il vous plaît : avant d’entrer dans l’épicentre du marché de la rechange de Bosch à Karlsruhe, en Allemagne, il faut d’abord franchir les obstacles de la protection de l’usine. Avec amabilité et dans la langue de Baden, nous sommes identifiés, photographiés, formés et signons toutes sortes de papiers. Elles disent : tout est secret ici. Le fait que nous puissions tout de même entrer et même prendre des photos – toujours après consultation, s’il vous plaît – est une exception exclusive. Car nous visitons ce qui ne se visite pas vraiment : le laboratoire de freinage de Bosch.
Le laboratoire de freinage se cache dans l’ombre de l’entrepôt central de l’aftermarket et porte le charme architectural d’une école primaire des années 1970. D’une certaine manière, c’est aussi très Robert Bosch GmbH : être au lieu de paraître ; dans ce bâtiment insignifiant d’un étage, ils en ont gros sur la patate en matière de technologie. Je m’appelle Andreas Mayer. Une poignée de main ferme et la ferme conviction que freiner, c’est bien plus que ralentir. Le titre officiel de la fonction de Mayer est « Product Area Owner (VP) ». Je vois. « Responsable de la zone de produits Freins Aftermarket », explique Mayer en souriant. En bref : Mayer est le chef. Et comme beaucoup ici, un vrai « Boschien » : stage, thèse, carrière – 20 ans de service. Ce natif de Hanovre n’a pas adapté le dialecte local, mais l’attitude locale : quand Bosch fait quelque chose, il le fait bien.
« Mieux vaut perdre de l’argent que de la confiance », comme l’avait dit autrefois Robert Bosch (1861 à 1942). Et a fondé en 1886, l’année de naissance de la voiture, l’entreprise qui a mérité cette confiance par la qualité – et parl’innovation. Le servofrein (1927), l’ABS électronique (1978), l’ESP qui en découle (1995) : toutes des premières mondiales de Bosch. Aujourd’hui, Bosch est le plus grand équipementier automobile au monde et le numéro un des systèmes ABS, par exemple. Etonnant : pour les plaquettes de frein (sur lesquelles nous nous concentrons ici), Bosch n’est pas un équipementier de première monte. En revanche, elle est le leader mondial des plaquettes de frein pour le marché de la rechange et, en Europe, des disques de freinage. Le programme de l’aftermarket comprend 46 000 articles de freinage. Parmi eux, des dizaines de liquides comme le nouveau DOT 4 E, un liquide de frein universel sans borates nocifs pour la santé et qui n’est donc plus une matière dangereuse. Ou 10 000 types de plaquettes de frein, couvrant 97 % du marché. Pour qu’il en soit ainsi, il y a trois laboratoires de freinage avec 120 collaborateurs : en Chine, aux États-Unis et au siège de l’aftermarket à Karlsruhe, en Allemagne.
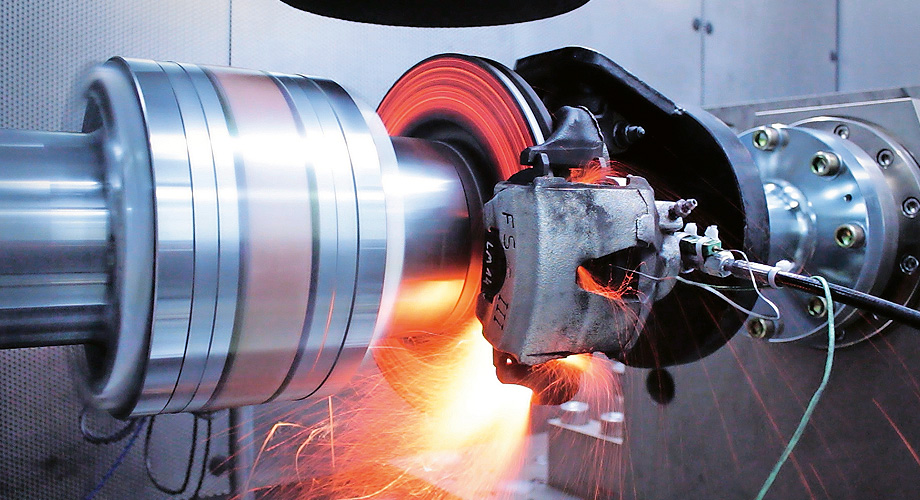
Tester jusqu’à ce que les disques de freinage soient littéralement incandescents : dans le laboratoire de freinage, les disques et les plaquettes sont soumis à de nombreux tests avant d’aller sur la route pour des essais réels. Les tests portent par exemple sur la résistance au cisaillement des revêtements, les vibrations et bien sûr les valeurs de frottement, c’est-à-dire de décélération. Photo : Bosch
Cuire des plaquettes de frein dans la cuisine
« C’est un peu comme la cuisine : au début, il y a les ingrédients », dit Mayer, 46 ans, avec un clin d’oeil, avant de nous conduire au laboratoire. Des creusets et des pots, des instruments scientifiques : ici, on analyse, on expérimente, on compose. Une cuisine dans laquelle l’équipe de Mayer assaisonne de nouvelles plaquettes de frein. Le développement de la plaquette de frein n’est-il pas terminé depuis longtemps ? Mayer nous regarde brièvement, comme si nous avions posé une question indécente, et répond : « Si nous arrêtions, nousserions hors du marché au bout de trois ans. Le frein est un élément sous-estimé. Une plaquette de frein est composée de 15 à 25 matériaux, et bien sûr, nous améliorons continuellement ». Qu’est-ce qu’il y a dedans ? Des métaux comme le fer ou le laiton, des choses imprononçables comme le sulfure de molybdène, souvent de l’aramide, du graphite, du kevlar, auxquels s’ajoutent des fibres de verre ou de caoutchouc et, pour ainsi dire, comme colle, des résines synthétiques et naturelles. « Et parfois du bois de hêtre », dit le cuiseur de garnitures de frein Mayer, en souriant et en savourant notre étonnement. Le bois peut ajuster la compressibilité. En d’autres termes, lorsque nous appuyons sur la pédale, le revêtement prétendument dur comme du béton doit être un peu compressible. S’il est trop dur, il grince. Cela ne devrait pas, estime Mayer, « surtout pas dans une voiture électrique silencieuse. Les grincements ne portent pas atteinte à la fonction, mais gênent les clients finaux. Cela ne correspondrait pas à l’idée que nous nous faisons de nous-mêmes ». Donc simplement des revêtements mous ? Si le revêtement est trop mou, la sensation de nos pieds devient spongieuse. « Il faut que ça fasse du bien, et les Européens aiment que leur frein soit mordant », explique Mayer. Ce qui nous permet de commencer à comprendre le conflit d’objectifs : chaque revêtement est une quadrature du cercle de freinage.
Une fois le compromis idéal trouvé, l’équipe de Mayer n’en a pas fini pour autant : pour l’Amérique, par exemple, il faut une sensation de pédalage douce. Sans parler des dispositions légales : en Europe, on s’attend à ce qu’une réglementation vienne un jour imposer que les revêtements soient exempts de cuivre. Les États-Unis l’exigent depuis longtemps – et à l’époque, Bosch était le premier fournisseur à s’y conformer. Depuis lors, chaque revêtement Bosch est exempt de cuivre et prêt pour une réglementation européenne correspondante qui suivra probablement. Non, les tâches ne manquent jamais ici. Chaque nouveau lot d’une matière première est contrôlé quant à sa composition et chaque lot de production est testé – ce qui signifie un contrôle mensuel pour les revêtements populaires. Mayer raconte ces choses de manière sympathique et décontractée et est quasiment une encyclopédie vivante sur les freins. Parfois, il glisse même « mes freins » au lieu de « nos freins ». Chez Bosch, ils prennent les freins personnellement. Dans la pièce d’à côté, un collaborateur glisse des plaquettes de frein fraîches dans un four comme un pâtissier ses biscuits. « Comme je l’ai dit, comme la cuisine », dit Mayer en riant, « dans le laboratoirenous mélangeons la pâte, ici nous cuisons la plaquette de frein sous pression et à la chaleur dans les mêmes conditions que plus tard dans la production en série ».
Une pièce plus loin : la chambre de torture. Ici, la pâtisserie est chargée jusqu’à ce qu’elle craque, au sens littéral du terme. Par exemple, lors du test de résistance au cisaillement : quelle est la tenue du revêtement sur la plaque de support ? Si le résultat est bon, le menu de freinage se déplace dans la halle avec des bancs d’essai encapsulés de la taille d’un conteneur outremer. Dans la salle de contrôle, les courbes et les chiffres défilent sur les écrans, les images thermiques montrent les températures sur des disques de freinage chauffés à 600 ou 800 degrés, tandis que sur le banc d’essai, même les climats allant de l’Arctique au désert et les nombreux cycles de conduite jusqu’à 250 km/h stressent les freins. Dans les rayonnages en hauteur, on trouve des axes comme les étagères Billy chez Ikea. Pourquoi les tests sontils effectués entièrement avec des suspensions de roues ? « Nous devons prouver pour chaque type de véhicule que la plaquette de frein pour ce véhicule précis satisfait à toutes les dispositions légales telles que la norme ECE R90. Et bien sûr, nos propres normes, qui vont encore bien au-delà des exigences légales », explique Mayer. Deux exemples : les vibrations ne sont pas réglementées par la loi, tout comme le fading ou la durée de vie des plaquettes au quotidien. Bosch établit donc ses propres règles pour cela, le dépassement est l’objectif.

Fidélité aux détails : selon les tests, des essieux complets avec amortisseurs et autres sont parfois montés sur des bancs d’essai. En effet, chaque pièce de frein du marché de la rechange doit être exactement adaptée au véhicule spécifique.
Euro 7 et la poussière de frein
Même l’air sortant des bancs d’essai est analysé. « Euro 7 », dit Mayer de manière laconique : des valeurs limites strictes pour l’abrasion des freins sont prévues vraisemblablement en 2027. L’industrie du freinage peut-elle y parvenir ? Mayer s’abstient de toute pique à l’égard des concurrents et déclare avec diplomatie « Il y a des revêtements qui peuvent le faire. Il faut simplement commencer assez tôt. Nos revêtements peuvent le faire » Les nouvelles réglementations sont-elles nerveuses ? non, nous considérons que nous avons une responsabilité à cet égard ». Ironiquement, ajoute Mayer, la poussière de frein est un sujet de préoccupation depuis bien plus longtemps aux Etats-Unis. Mais pas pour des raisons environnementales : les clients américains ne détestent rien de plus que des jantes sales sur leur véhicule rutilant. C’est la fin de notre visite. Et pour les revêtements, les tests ? « Pas du tout », souligne Mayer en montrant l’extérieur, où la flotte de voitures, de la VW Polo au Mercedes Sprinter, est prête à partir à l’assaut du Jura souabe, du Grossglockner ou du Stelvio – parce que la réalité imagine toujours des martyres bien plus méchants que n’importe quel banc d’essai. « Lors du test sur route, nous traitons les freins comme il ne faut pas les traiter. Et il faut que ça fasse du bien. Cette partie subjective ne peut pas être quantifiée », explique Mayer. Si les plaquettes, disques et autres maîtrisent cette étape, la production en série est autorisée (ce que Bosch fait lui-même dans quatre cinquièmes des cas de plaquettes de frein). Et si ce n’est pas le cas ou si, lors d’un seul des nombreux tests, le frein ne freine pas bien une seule fois ? Tout recommence.
Au fait, combien de temps cela prend-il ? « La plupart du temps, environ trois ans ». Est-ce que cela en vaut la peine ? Manifestement : il y a quelque temps, l’UE a effectué des contrôles aléatoires. Près de la moitié des revêtements ont été recalés parce qu’ils ne répondaient pas aux exigences minimales légales. « Les nôtres n’y étaient pas », dit Mayer, l’air satisfait. Pas étonnant que tout soit secret ici : la concurrence viendrait volontiers jeter un coup d’oeil. Car chez Bosch, on brûle pour ses freins. Robert Bosch aurait certainement apprécié le laboratoire de freinage.
Ajouter un commentaire
Commentaires